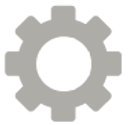

ALLISTAIR COTA
DESIGN PORTFOLIO
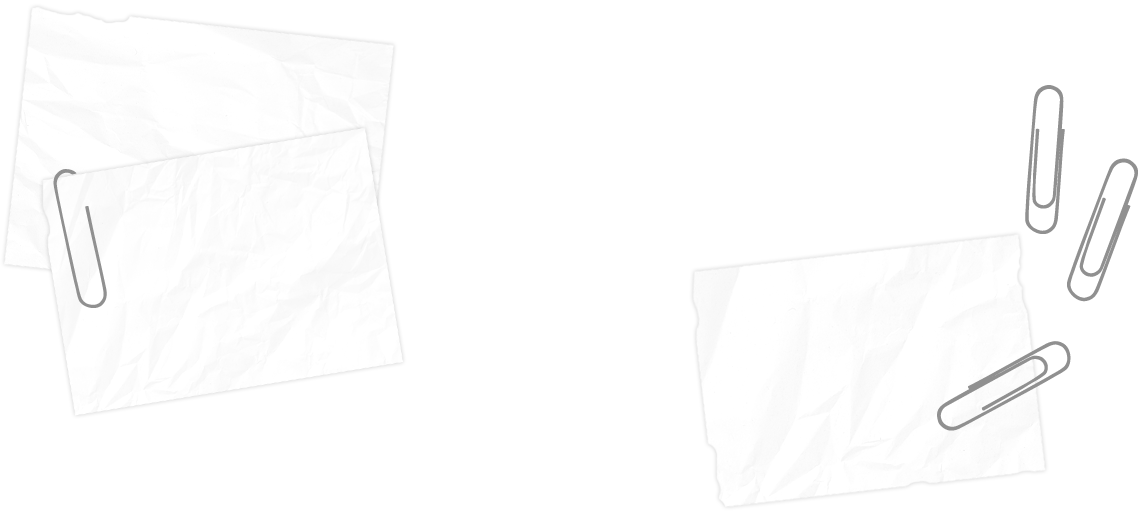

Harrington Rod Hook
As part of the Manufacturing Engineering project, my team was tasked with preparing a report outlining the process of manufacturing a hook of a Harrington rod using lost foam casting and electric discharge machining (EDM) methods. The report would include descriptions of how each method would produce the features of the part, and engineering drawings of the various steps in each process
Background
The Harrington rod was a surgical device that was implanted along spinal columns of scoliosis patients from the late 1960s to early 1990s. The part we were assigned to discuss in our report was a hook of the rod that would be
used to secure the rod onto the vertebral laminae. The assignment stated that the part had to be made from a plastic clamp within three days, hence the lost foam casting and EDM processes were the most suitable to manufacture the part. However, an investigation had to be included in the report about the best casting method that could mass manufacture the product.


Design Decisions
The plastic cable clamp was suggested as the pattern to be used in the lost foam casting process, which would evaporate after the molten metal was poured into the pouring cup. The through hole was to be made using EDM. External view orthographic drawings were produced to outline the steps in each process.
One of the challenges we faced was choosing the best location for locating the pouring cup and sprue. This decision was made by calculating the time taken by the molten metal to solidify in each section of the part, and then identifying the appropriate location and dimensions of the sprue which would ensure the whole part experienced solidification of molten metal before the sprue. Once this decision was made, we generated a CAD model of the part with the pouring cup and sprue attached using SolidWorks.
CAPTION
Mass Production of the Hook
Our team decided that the main objectives that the mass manufacturing process should achieve were to make the part at a low cost, to achieve low dimensional tolerances, and to produce smooth surface finish for the part. Other objectives included mold reusability, short set-up times, and high part complexity. The candidate casting processes included sand, die, investment, and lost foam casting. With the help of a weighted decision matrix that was developed based on a set of criteria, investment casting was chosen to be the best process to mass manufacture the hook of the Harrington rod.
The Team:
-
Abhirav Kotwal
-
Alain Cubric
-
Allistair Cota
-
Samson Chiu
