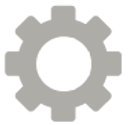

ALLISTAIR COTA
DESIGN PORTFOLIO
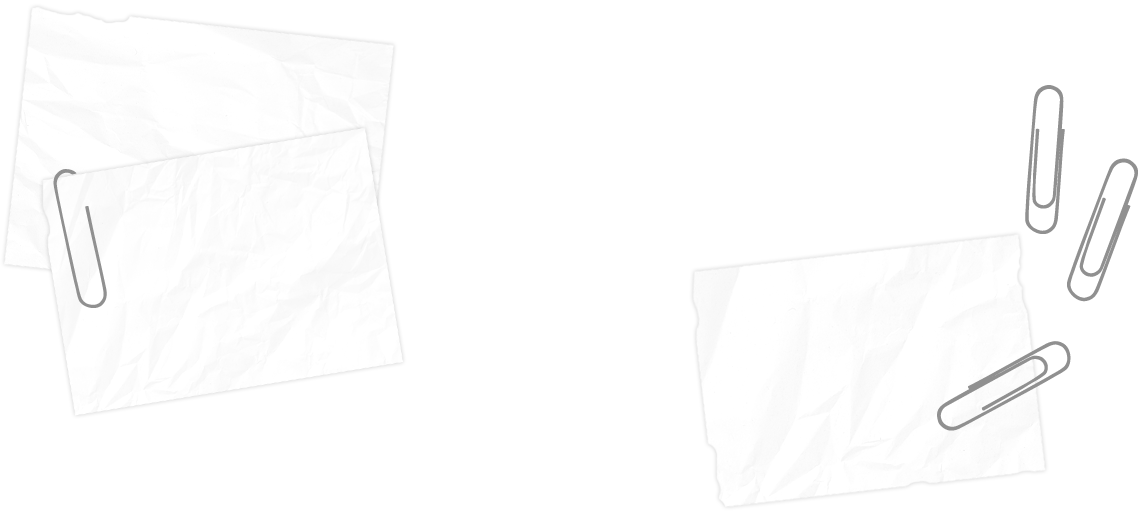
Casement Window Crank Operator
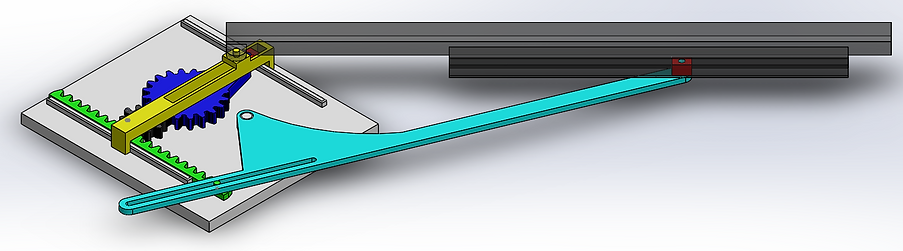
For the design project of our Kinematics and Dynamics of Machines course, we were tasked with identifying a deficiency within an existing kinematic mechanism in a machine or product, and suggesting an upgraded design which would eliminate this deficiency based on a full kinematic analysis of both designs. My team decided to improve the casement window crank operator mechanism. The deficiency we identified with casement windows was that when the window is fully open or closed (i.e. at its limit positions), a significantly greater amount of torque is required to turn the crank. This poses a problem mainly for the elderly and consumers with ailments that inhibit the physical exertion of an arm, wrist or hand. Thus the objective of the new design was to facilitate window opening and closing by allowing the window to be opened with a lower input force supplied to the crank, while maintaining the same stroke and motion during operation.
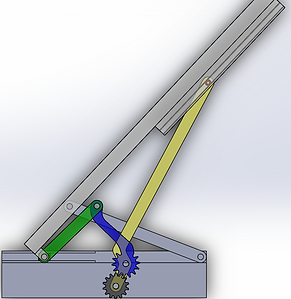

Left: SolidWorks assembly of the existing mechanism.
Right: Components of a casement window crank operator [1].
In the existing mechanism, during the opening stroke, a modified slider crank mechanism driven by a planetary gear train pulls the window along its retainer clip along a hinge channel, while the other end of the window is simultaneously pushed outward by a crank arm. One of the main issues with this mechanism is that the links are placed parallel to each other in their limit positions, thus necessitating greater force to restart the motion and break free from the parallel configuration.
The new design replaced the planetary gear train with a rack and pinion gear set. A scotch-yoke mechanism replaced the slider crank for moving the window along the hinge channel, while the crank arm was redesigned with a groove that allowed a pin from the rack to slide through and push on the walls of the groove. This design reduced the number of links that were collinear and parallel at the limit positions.
Using the Working Model 2D software, it was confirmed that the new design would produce a stroke and motion similar to the old design, thus keeping with the design constraints. To evaluate the performance of the new design against the existing mechanism, graphical force analysis at a representative instant during the motion was conducted to find the required input torque on the crank. The new design required significantly less torque (60% less) than the existing mechanism thus achieving the primary objective of the design in facilitating window opening and closing.

SolidWorks assembly of the new design.
The Team
-
Alain Cubric
-
Samson Chiu
-
Jonathan Swiecki
-
Allistair Cota
[1] The Family Handyman. (2014). How to Repair Old Windows [Online]. Available: http://www.familyhandyman.com/windows/repair/how-to-repair-old-windows/view-all
