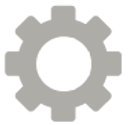

ALLISTAIR COTA
DESIGN PORTFOLIO
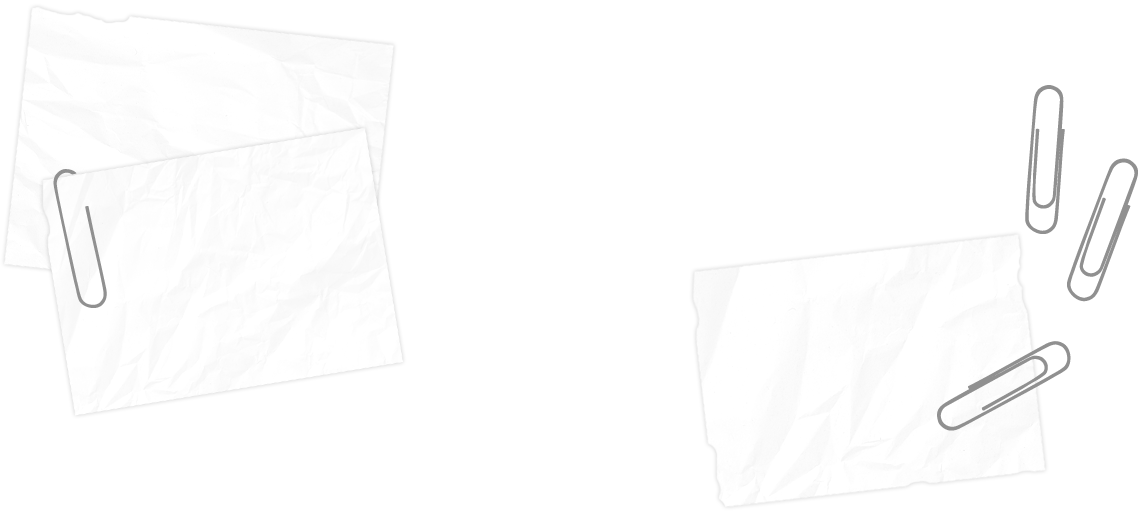
Curb Climbing Powered Wheelchair
As part of my final year Capstone Design project, our team was tasked by the Mechanics and Aerospace Design Laboratory (MADL) at the University of Toronto with designing an innovative powered wheelchair. Due to the open-ended nature of the project, the team set out to determine the innovative functions of the design by meeting with occupational therapists and physiotherapists, along with wheelchair retailers and end-users. After reviewing the issues highlighted in these meetings along with research from a literature review, the team decided to design a powered wheelchair that offered improvements in the three challenge areas:
-
traversing curbs
-
portability
-
cost
​
Final Design Description
The final design performs curb traversal thanks to a Tri-Wheel mechanism, which replaces a standard wheel on a typical powered wheelchair and consists of a triangular arrangement of wheels supported by a triangular-shaped bracket and driven by a planetary gear train. Portability is achieved via the modular design of the wheelchair, which can be disassembled easily by the user into four main sub-assemblies (seat, batteries, left and right chassis halves). A seat-leveling mechanism is also included to minimize the amount of seat tilt experienced by the user during steep curb climbs.
Team
-
Samson Chiu
-
Allistair Cota
-
Alain Cubric
-
Prasanth Gopinath
Engineering Design and Analysis
Finite element analysis (FEA) via ANSYS Workbench was used to evaluate the stresses experienced by critical components to ensure functionality and safety. To aid in portability, material selection charts (also known as Ashby charts) were generated using the Cambridge Engineering Selector (CES) software used to choose materials that minimized weight and cost of large components while still meeting constraints including structural integrity and durability. SolidWorks was used to create the 3D CAD assembly of the final design and engineering drawings for every custom component. Dynamic analysis of the driving and curb climbing scenarios was performed to guide the selection process of the drive motors and planetary gear train ratios. MATLAB and Simulink were used to model the suspension system and determine a suitable spring constant and damping coefficient for the suspension shock absorbers. Kinematic analysis of the climbing scenario was performed to select an appropriate actuator for the seat-leveling mechanism. The client was provided with a complete Bill of Materials (BOM), including all custom and off-the-shelf components (both mechanical and electronic components), with engineering drawings for custom parts, assembly drawings for main sub-assemblies, and datasheets for off-the-shelf components. An electrical schematic for the interfacing of all electronic components was also developed using Autodesk Eagle and provided to the client.
Showcase Prototype
For the Capstone showcase event, the team built a scaled-down proof of concept prototype (approximately 1:3 scale) that demonstrated the curb traversal and portability capabilities of the design. Custom components including the chassis and tri-wheel brackets were 3D printed, while hobby level electronics (motors, h-bridges, gyro, actuator) were utilized. An Arduino UNO microcontroller board was used to convert the user input from a Nintendo Wii Nunchuck into appropriate drive commands, while also activating the seat-leveling actuator based on the readings from the gyro that was mounted to the seat.
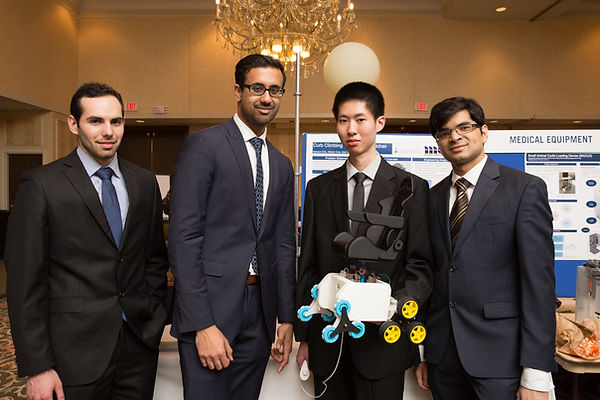


Left: CAD model of the final design.
Right: The wheelchair climbing a curb.
The team and the prototype:(from left to right) Alain, Prasanth, Samson and myself
